We also recommend suitable grades according to customer demand.
We make according to customer's drawings.
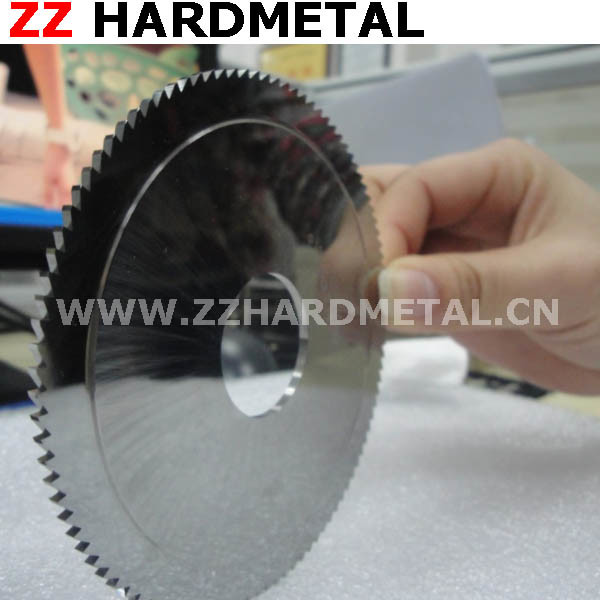
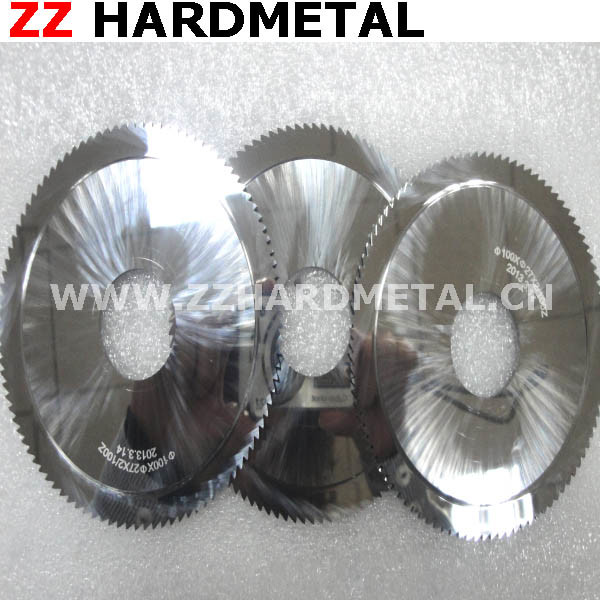
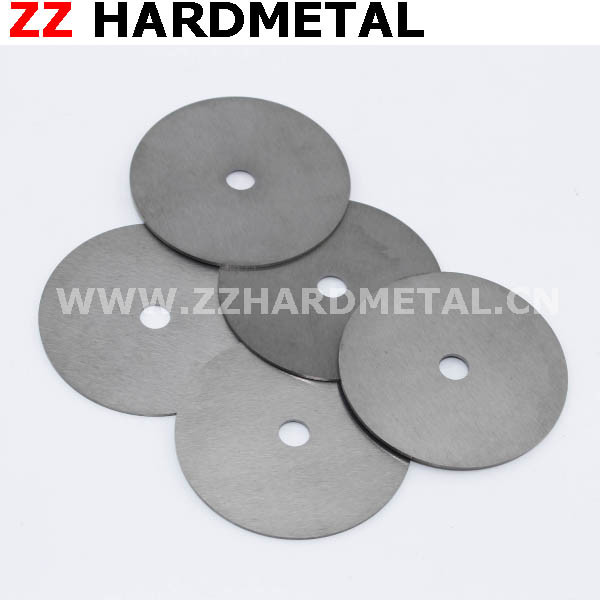
High precision circular disc cutter, round-cut blades (high wear / sharp / stainless)
1, Tolerance: High Availability to diameter (± 0.01) * Thickness (± 0.005) * inner diameter (H7) * balance (± 0.005)
2, Hardness: HRC64 ° ~ 66 ° And HRC68 ° ~70 °
3, Features: Cutting blade requires precision diameter, thickness, straightness, etc. Customized are also welcomed!
YG8 and YS2T are widely used for making carbide cutting disc. But other size can be offered by your requirement.
Grade properties:
YG8: High strength in use, impact and shock resistance higher than YG6, but wear resistance and cutting speed comparatively lower. Roughing of cast irons, non-ferrors metals and their alloys as well as non metallic materials at low cutting speed.
YS2T: Fine grade alloy, with high wear resistance, high bending strength, high resistance to bonding, high thermal strength. Machining of refractory alloys, stainless steel and high manganese steel, etc.
Ways to identify good carbide disc
1. Sound checking: Before installing the blade, hang the blade with fingers. Gently knock with a wooden hammer, listen to sounds, it is cracked if muddy sound, prohibited to use if cracked, in order to avoid accidents!
2. Running speed: Make sure the cutting speed is in or below 4800 rev/min.
3. Blade install: When installing, rotating shaft and blade center requires accurate alignment of the blade, clean the mechanical mounting surfaces, no cutting material, dust or other debris to be left on blades.
4. Install protective devices: You must install the protective cover (blades should baffle around the studio, steel, rubber and other protective equipment) before the blade running.
ZZ HARDMETAL provides the followings as a guide to satisfy you:
Availability
Durability
Rust resistance
Cutting process
Costs
Edge geometry
Wear resistance
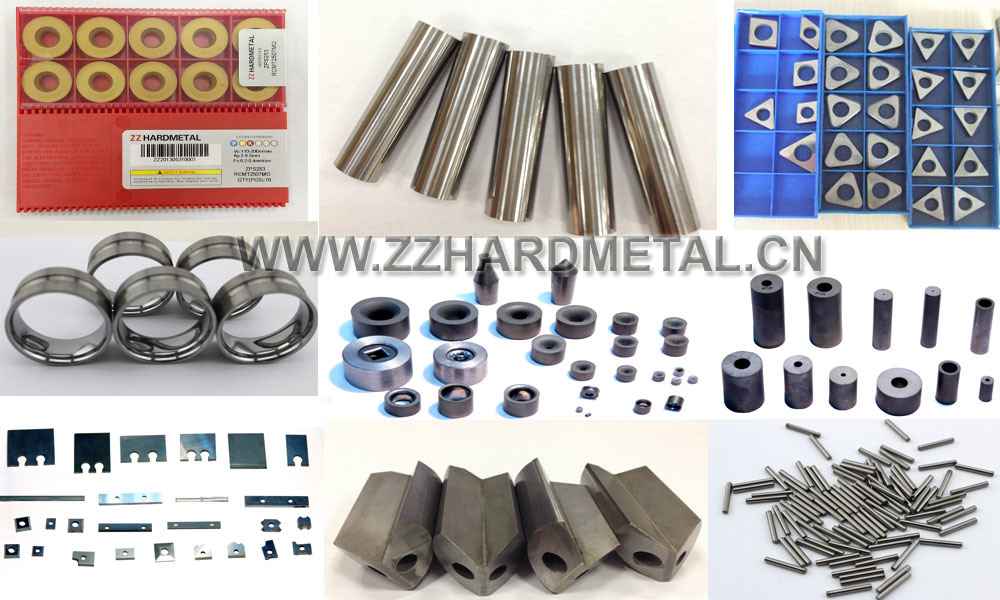
We also recommend suitable grades according to customer demand.
We make according to customer's drawings.
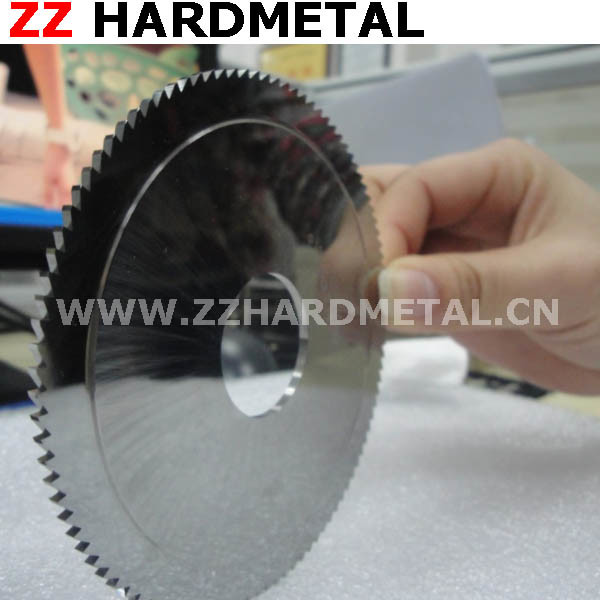
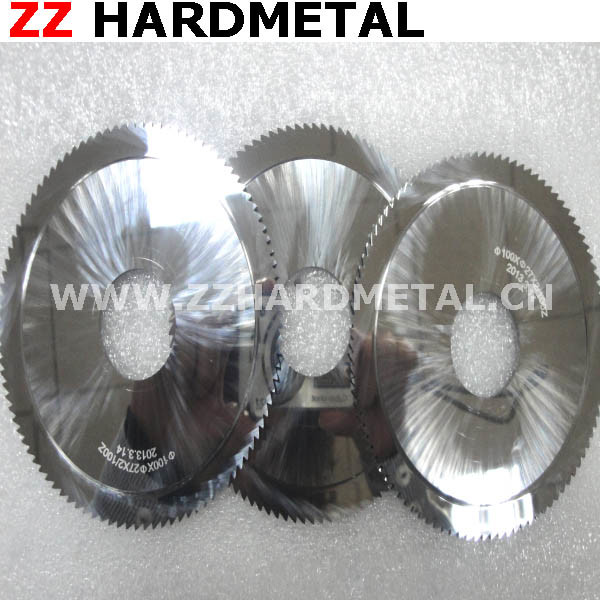
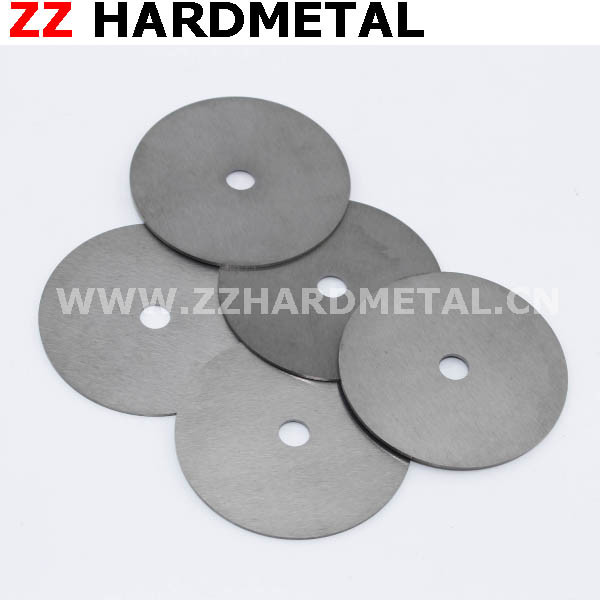
High precision circular disc cutter, round-cut blades (high wear / sharp / stainless)
1, Tolerance: High Availability to diameter (± 0.01) * Thickness (± 0.005) * inner diameter (H7) * balance (± 0.005)
2, Hardness: HRC64 ° ~ 66 ° And HRC68 ° ~70 °
3, Features: Cutting blade requires precision diameter, thickness, straightness, etc. Customized are also welcomed!
YG8 and YS2T are widely used for making carbide cutting disc. But other size can be offered by your requirement.
Grade properties:
YG8: High strength in use, impact and shock resistance higher than YG6, but wear resistance and cutting speed comparatively lower. Roughing of cast irons, non-ferrors metals and their alloys as well as non metallic materials at low cutting speed.
YS2T: Fine grade alloy, with high wear resistance, high bending strength, high resistance to bonding, high thermal strength. Machining of refractory alloys, stainless steel and high manganese steel, etc.
Ways to identify good carbide disc
1. Sound checking: Before installing the blade, hang the blade with fingers. Gently knock with a wooden hammer, listen to sounds, it is cracked if muddy sound, prohibited to use if cracked, in order to avoid accidents!
2. Running speed: Make sure the cutting speed is in or below 4800 rev/min.
3. Blade install: When installing, rotating shaft and blade center requires accurate alignment of the blade, clean the mechanical mounting surfaces, no cutting material, dust or other debris to be left on blades.
4. Install protective devices: You must install the protective cover (blades should baffle around the studio, steel, rubber and other protective equipment) before the blade running.
ZZ HARDMETAL provides the followings as a guide to satisfy you:
Availability
Durability
Rust resistance
Cutting process
Costs
Edge geometry
Wear resistance
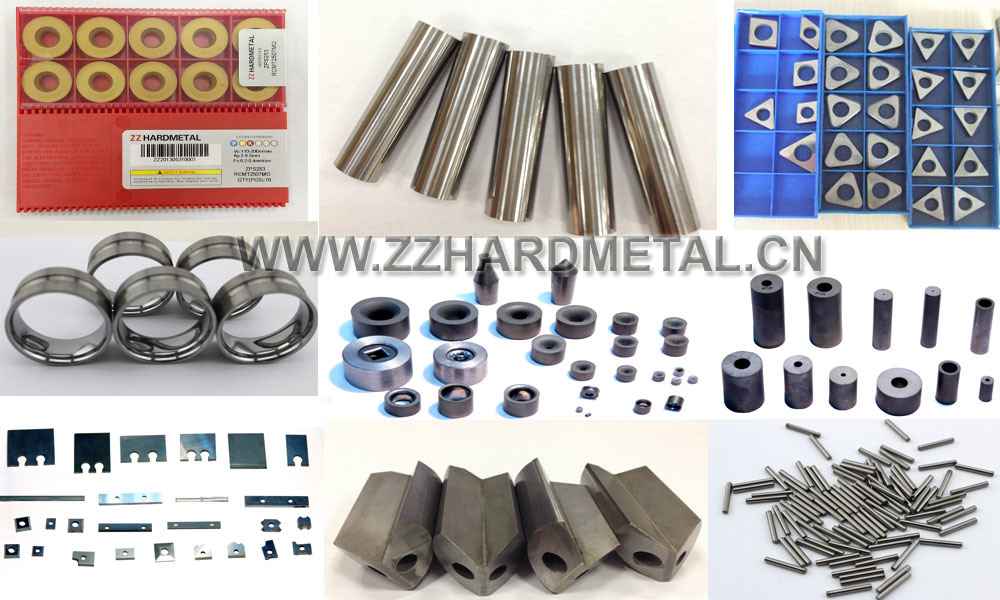
Hook Type Ring Winding Machine
The common functions of Automatic Winding Machine include preset number of turns, automatic stop, positive and negative winding, automatic slot crossing, etc. in actual use, we should pay attention to several points. First, start winding idle and stop winding idle. Start winding idle is the function of slow running after starting the equipment, so as to reduce the impact on tension structure and enameled wire, Generally, it can be set as 1 to 3 turns according to the actual needs. The stop and idle function is that the equipment runs at a slow speed before ending the winding sequence. This function can reduce the impact on the brake and make the equipment finish winding smoothly, especially for the winding process that needs precise positioning. This parameter must be set according to the running speed of the equipment, The parameters should also be adjusted accordingly. Generally, it is 2 to 5 turns, and then the winding direction and the winding direction. These two parameters are respectively the setting of the winding displacement direction and the spindle rotation direction. The winding axis and the spindle of the automatic winding machine are controlled by the controller, and there is a specific linkage relationship. When setting, the displacement direction of the winding axis must be clear, Many users report the equipment alarm during debugging, which is due to the equipment protection caused by the wrong setting. The winding machine has a zero detection point, which is used to position the winding shaft. If the equipment is started from the zero point, the winding shaft must move outward. If the equipment is set to move inward by mistake, it will cause the equipment alarm. The rotation direction of the winding shaft should be determined according to the winding process, All settings should fully consider the needs of winding process.
Hook type ring winding machine, semi automatic ring winding machine, wire coil winding machine
SUZHOU DEGU MACHINERY CO.,LTD , https://www.deguwindingmachine.com