The main components of a lead storage battery are as follows:
Anode plate (lead peroxide. PbO2)---> Active material Cathode plate (sponge lead. Pb) ---> Active material Electrolyte (diluted sulfuric acid) ---> Sulfuric acid ( H2SO4) + Water ( H2O)
Battery case, isolation plate, other (liquid port plug, cover, etc.)
Principle of lead storage battery The anode (PbO2) and cathode (Pb) in the lead storage battery are immersed in the electrolyte (dilute sulfuric acid), and 2V of electricity is generated between the two poles. According to the principle of the lead storage battery, the cathode and cathode are charged and discharged. The electrolyte changes as follows:
(anode) (electrolyte) (cathode)
PbO2 + 2H2SO4 + Pb ---> PbSO4 + 2H2O + PbSO4 (discharge reaction)
(lead peroxide) (sulphuric acid) (sponge lead)
(anode) (electrolyte) (cathode)
PbSO4 + 2 H2O + PbSO4 ---> PbO2 + 2 H2SO4 + Pb (Charging reaction)
(lead sulphate) (water) (lead sulphate)
1. Chemical change during discharge When the battery is connected to an external circuit, the dilute sulfuric acid reacts with the active substances on the anode and anode plates to form a new compound, “lead sulfateâ€. It is released from the electrolyte via the discharge sulfuric acid component, and the longer the discharge, the thinner the sulfuric acid concentration. The consumed component is proportional to the amount of discharge. As long as the concentration of sulfuric acid in the electrolyte is measured, that is, the specific gravity is measured, the amount of discharge or the amount of residual electricity can be known.
2. The chemical change in charging occurs because the lead sulfate produced on the anode plate during discharge is decomposed and reduced to sulfuric acid, lead and lead peroxide during charging, so the concentration of the electrolyte in the battery gradually increases, that is, The specific gravity of the electrolyte rises and gradually returns to the concentration before discharge. This change shows that the active material in the battery has been reduced to a state in which it can be re-powered. When the lead sulfate of the two poles is reduced to the original active substance, it is equal to At the end of charging, the cathode plate produces hydrogen, and the anode plate generates oxygen. When charging to the final stage, the current is almost always used in the electrolysis of water, so the electrolyte is reduced. In this case, it should be replenished with pure water.
Waste Engine Oil Distillation Plant
The Waste engine Oil Distillation Plant is used to refine waste engine oil, crude oil and fuel oil after pyrolysis process into diesel grade oil, gasoline or and base oil. The daily capacity of this plant is about 5-6 tons.
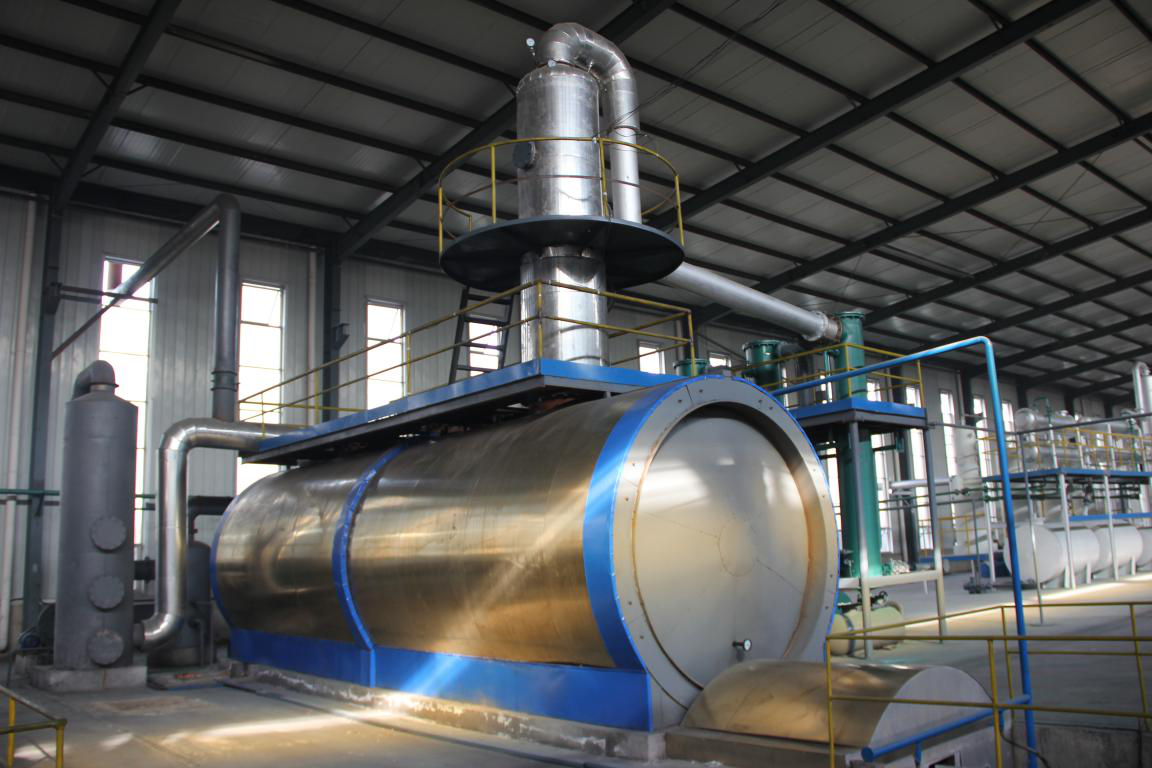
Flow-chat of waste engine oi Distillation Plant
Advantage of waste engine oi distillation plant
1. Unique and original manufacturing and technology with our own formula of our equipments in China;
2. Unique horizontal design, high oil output with about 90% oil yield and 100% conversion rate, highly effective and profitable;
3. Good quality end product oil as the substitution of standard diesel oil in usage;
Automatic submerged welding technology, ultrasonic nondestructive testing, both manual and the automatic safety devices;
4. Sync gas recycling system: fully burned after recycling and utilization, saving fuel and preventing pollution;
5. National patent, unique heat insulation shell: high efficiency temperature keeping, excellent energy-saving effect;
6. High condensing efficiency condensers with more oil output. Good quality oil, longer lifetime, and easy to clean;
7. National patent water film smoke scrubbers: efficient removal of the acid gas and dust of the smoke, environmental friendly to meet related national standards.
Technical Parameter of Waste engine Oil Distillation plant
NO. |
Item |
Technical Parameter |
1 |
Suitable Raw Materials |
Waste engine oil, Pyrolysis fuel oil, crude oil |
2 |
Structure |
Horizontal Type |
3 |
Capacity(24 hours) |
3.5-6.5Mt |
4 |
Work Pressure |
Normal Pressure |
5 |
Oil Yield |
80%-90% |
6 |
Power |
18 kw/H |
7 |
Cooling Method |
Cycle water |
8 |
Condensers |
4 pieces of Vertical condensers |
9 |
Emission Treatment |
New DE-sulfurization Smoke Scrubbers |
10 |
Heating Method |
Hot Air |
11 |
Type of Installation |
With Foundation |
12 |
Noise dB(A) |
≤85 |
13 |
Dimension of Reactor(mm) |
Ф2200×6000 Ф2500×8800 |
14 |
Operating Mode |
Semi-continuous Operation |
15 |
Main Chamber Weight (MT) |
10~13Mt |
16 |
Total Weight(MT) |
25~35Mt |
17 |
Installation Space Required |
35m*15m |
18 |
End Product |
Non-standard diesel oil |
19 |
Manpower |
1~2/shift |
20 |
Shipment Requirement |
2*40HC=Ф2200×6000 1*40HC+1*40FR=Ф2500×8800 |
Waste Engine Oil Distillation Plant
Distillation Plant,Oil Distillation,Waste Oil Recycling,Waste Engine Oil Recycling
Shangqiu Jinpeng Industrial Co., Ltd. , http://www.recyclingthewaste.com