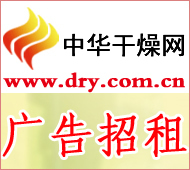
China Drying News reported that after more than 10 days of operation data analysis, the weight of heavy alkali water dropped from the original 18% to the current 13% or less, and tons of alkali can save more than 150 kilograms of medium-pressure steam consumption.†January 31, Shandong Sea Wu Huannan, manager of Technical Department of Soda Ash Plant, said at the site of the second line dehydration project at the soda ash plant's new line of heavy alkali. At present, Haihua Soda Ash Plant has used 21 centrifuges, which can save more than 40,000 tons of standard coal in the whole year.
Soda ash production uses a steam drying and calcination process, and steam consumption accounts for about 75% of the total energy consumption of soda ash production. The level of heavy alkali water directly affects the consumption of calcined steam. Under normal circumstances, the heavy alkali water is about 18%, and for each 1 percentage point reduction, 1 ton of soda ash can reduce 30 kg of calcined steam consumption.
The second-phase heavy-alkali dewatering reform project of Haihua Soda Ash Plant New Line adopted a high-efficiency energy-saving centrifuge and adopted DCS. After one year of design, construction, commissioning, and rectification, it was successfully commissioned on January 17th. The technology adopts the secondary dehydration of the wet and heavy alkali after the process of the filter alkali machine, which not only reduces the heavy alkali water and steam consumption, but also improves the capacity of the calciner, reduces the salt content of pure alkali, and improves the product quality.
The project was selected as the second batch of national resource conservation and environmental protection projects, and it received 7.8 million yuan of financial subsidy funds from the state's central budget.
Haihua Soda Ash Plant had imported 8 sets of high-tech centrifuges from Germany in 2008, and implemented a heavy alkali secondary centrifugal dewatering transformation on the old line. The annual energy consumption was reduced to 17,100 tons of standard coal, becoming the first in the industry in the country. The successful use of centrifugal dewatering technology, energy-saving soda ash production enterprises.
A rectifying tower is an equipment used to separate different components in a mixture. It utilizes the boiling point differences of different components to gradually separate the components in the mixture through alternating heating and cooling. Distillation towers are commonly used in industries such as oil refining, chemical engineering, and pharmaceuticals, for purifying chemicals, separating petroleum products, and preparing pharmaceuticals.
The characteristics of the rectifying tower include:
1. Efficiency: The rectifying tower can separate the components from the mixture in a short period of time, improving production efficiency.
2. High precision: The rectifying tower can separate high-purity chemicals or petroleum products, ensuring product quality.
3. Strong flexibility: The rectifying tower can perform different operations according to needs, and can be operated continuously or intermittently to adapt to different production needs.
4. Energy conservation and environmental protection: The rectifying tower adopts a closed loop heating method, which can save energy and reduce environmental pollution.
Multifunctional Rectifying Tower,Continuous Rectifying Tower,Plate Rectifying Tower,High Efficiency Rectifying Tower
Yangzhou Tongyang Chemical Equipment Co., Ltd. , https://www.tongyangchemic.com