Many workpiece surfaces are highly polished, and slight tool contact measurements can damage the surface of the workpiece. Many workpieces are deformed under slight external forces due to material or structural factors, making it virtually impossible to achieve high-precision measurements. When measuring tools such as calipers and micrometers, there are certain requirements for the use of these measuring tools for measurement personnel. If the measurement cannot be performed, errors in the measurement itself will occur. In particular, measuring tools that require human readings will result in deviations. Will be bigger. Generally, the workpiece will have a plurality of dimensions to be measured. If it is operated in a contact manner, only one dimension can be measured at one time. This results in a lot of repetitive tasks in the measurement process, which greatly reduces the detection efficiency. .
Many limited problems with contact measurement affect the accuracy and efficiency of industrial measurements. With the rapid development of industrial automation, how to minimize the influence of human factors on product quality stability is an issue that every manufacturing enterprise cannot avoid. The application of machine vision in the field of measurement happens to be a very effective solution to these problems. In line with automated production lines, the products are accurately and efficiently measured, sorted, and connected to front-end and back-end automation workstations through image processing. They are perfect for processing, inspection, screening, positioning, assembly, packaging, and storage. Link.
At present, the status of production models and production equipments of domestic industrial manufacturing enterprises is uneven, and each enterprise has different measurement requirements for products at different production stages. Machine vision is currently measured on domestically specialized workstations or laboratory benchtops. The main instrument products. Laboratory benchtop measurement instruments are fixed standard products that can only be measured statically, and have fixed matching limits on the field of view of the shooting. The station-based measurement equipment specifically designed on the production line is mostly based on the directional detection requirements of different companies. The non-standard customized development is highly targeted and can work dynamically. However, such equipment is often unable to continue to be used due to upgrading or retrofitting of enterprise products, resulting in relatively large waste of resources. Therefore, how to combine vision measurement and industrial automation standard equipment on the production line is an important problem solving direction.
We know that the current visual hardware for machine vision measurement is mainly the combined mode of telecentric lens + parallel light source, because it can extract the depth outline of the image with the most accurate distortion, and the accuracy result during the work process. It will not be affected by changes in ambient light, high-frequency vibration in the production line, or the positioning of the workpiece on the assembly line. Being able to meet these very realistic usage requirements in itself illustrates the irreplaceability of this hardware combination. But why is such a combination method not well matched with a mature mechanical arm to achieve an ideal use effect? The most important reason is that the product volume of telecentric lenses and parallel light is relatively large. The main reason is that the length is very long, and the cylindrical contour is not good for positioning the optical axis. If the optical axis is adjusted inconveniently, it will be very useful. Trouble. The combination of these reasons makes the flexible configuration of the robot + optical system on the production line unrealistic.
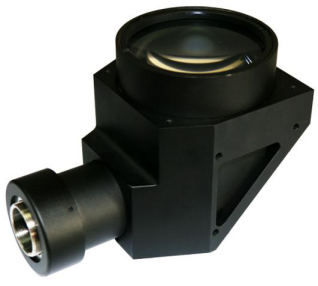
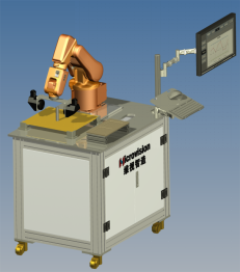
In response to this problem, BTOS made targeted technological breakthroughs in product development and developed the BT-ZF series of double telecentric lenses and parallel light source products. Compared with conventional telecentric products, they have reduced the length of their appearance by more than 50%. And can be a variety of positioning and installation, only need to lock the screws, no need to make clamps or other institutions positioning, the camera interface introduces a new idle mechanism, easy to adjust the angle and direction of the image after the installation of the lens, greatly optimizing the use of convenient Sex.
Pasteurized Milk Processing Line
Jump Machinery (Shanghai) Limited is a modern high-tech joint stock enterprise specialized in the turnkey production line of concentrated juice, jam, pulp, tropical fruits, herb and tea beverages, carbonated drinks, wine, beer, yogurt, cheese, milk, butter etc. At the same time, Jump is also committed to manufacturing various food machinery, such as Can Food Machinery , Fruits Juice Machinery, Tomato Sauce Machinery, Fruits Jam Machinery, Dairy Machinery etc.
Jump is able to supply service from A to Z about your project, not only machine manufacturing, installation commissioning, technical training, after-sales service, but also before-sales service, including factory building construction drawings, facilities layout, and water, electricity, boiler steam. Jump has a professional team to help clients to design the layout on worksite and draft the implementation plan, program schedule and expense estimation in each stage of the project until the production line starts the project.
As an industry leader, it has the best projects, professional engineers and technicians, strong R&D department with a number of masters and PhD of food engineering & packaging machinery, stable long-term development and highly rated customer experience in every province in China and also in Africa, the Middle East, Southeast Asia, Oceania, Europe and America.
Pasteurized Milk Processing Line,Pasteurized Milk Production Line,Pasteurized Milk Machinery,Pasteurized Milk Processing Machinery
Jump Machinery (Shanghai) Limited , https://www.shanghaimachineries.com