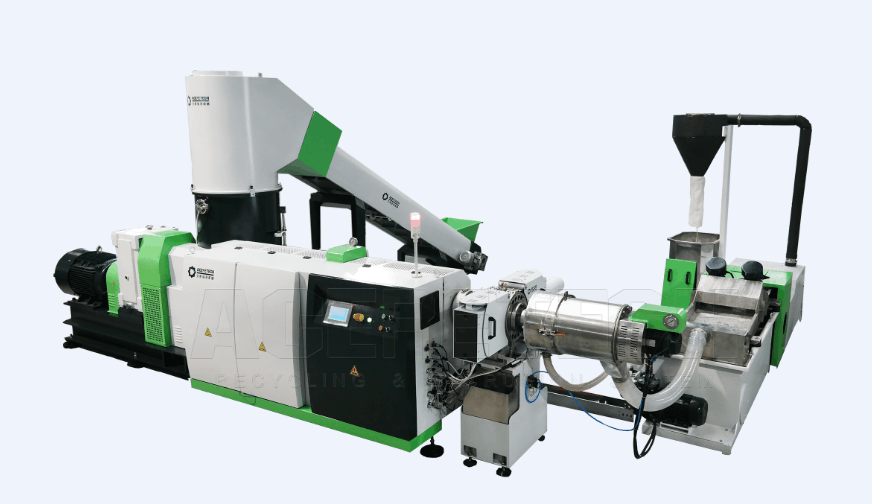
The ACS series compacting and pelletizing system combines function of crushing, compacting, plasticization and pelletizing to one step, applied in the plastics recycling and pelletizing process. ACS system is a reliable and efficiency solution for PP/PE/PET/PVCÂ films, raffias, filaments, PP woven/non woven bags and EPE/EPS/XPS foaming materials re-pelletizing.
Final productions produced by ACS system are in the form of pellets/ granules, can directly put into the production line for film blowing, pipe extrusion and plastics injection, etc.
Specifications:
Model Name | ACS |
Recycling Material | HDPE, LDPE, LLDPE, PP, BOPP, CPP, OPP, PA, PC, PS, PU, EPS, PET |
Final Product Shape | Pellets/ Granules |
System Composition | Belt conveyor, cutting compactor, single screw extruder, pelletizing device, water cooling unit, dewatering section, conveying blower and production silo |
Output Range | 160kg/h-1200kg/h |
Feeding Device | Belt conveyor (standard), Rolls hauling off device (Optional) |
Compactor Volume | 300 Liters-1400 Liters |
Screw Diameter | 80mm-180mm (standard) |
Screw material | 38CrMoAlA nitride steel( SACM-645), bimetallic ( Optional) |
Screw L/D | 34/1, 36/1 (depending on features of recycles) |
Barrel's Heating | Ceramic heater or Casting Aluminum heater |
Barrel's Cooling | Air cooling through fan blowers |
Vacuum Degassing | Double vented degassing with roots pump unit(Standard)Â |
Pelletizing Type | Water cooling strands pelletizing system |
Voltage Standard | Depending on project's location |
Optional Devices | Metal detector, rolls hauling off device, micro feeder for masterbatch, additives, chiller, etc. |
Delivery Time | 60 days after order takes effect. |
Warranty | 13 months since date of bill of lading |
Technical Service | Project design, suggestion on factory construction, installation and commissioning |
Working steps of ACS compacting and pelletizing system
Â
Â
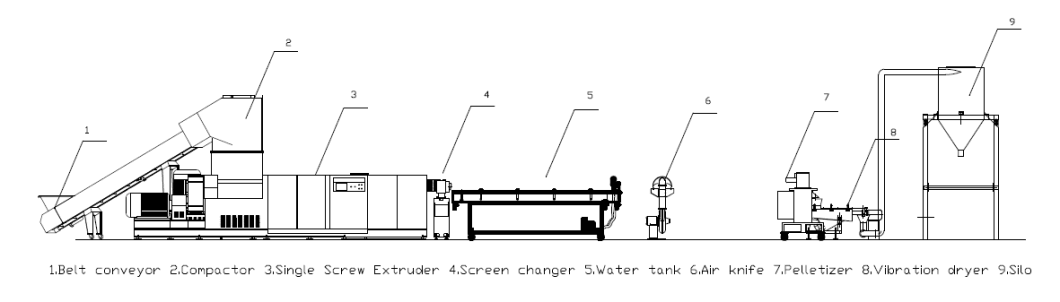
1. Feeding:Â as standard design, plastic scraps such as film, filament, raffias conveyed into the compacting room through belt conveyor; to handle rolls' scraps, roll hauling off device is an optional feeding method. Motor drives of conveyor belt and hauling device cooperate with ABB inverter. Feeding speed of conveyor belt or roll hauling off is fully automatic based on how full the compactor's room is. Metal detector can be combined with belt conveyor, and can interlock with control system, to warn and stop the system, in case that metal is found in feeding section.
2. Crushing and compacting:Â the rotatory blades of compactor will cut up incoming scraps. Frictional heating which caused by high speed rotatory blades will heat and let scraps shrinking just below their agglomerating point. Optimal designed guide structure compacts the material and directs it into extruder screw. Crushes, dries and compacts the material which enables a fast and stable feeding from the compactor directly into the extruder.
Â
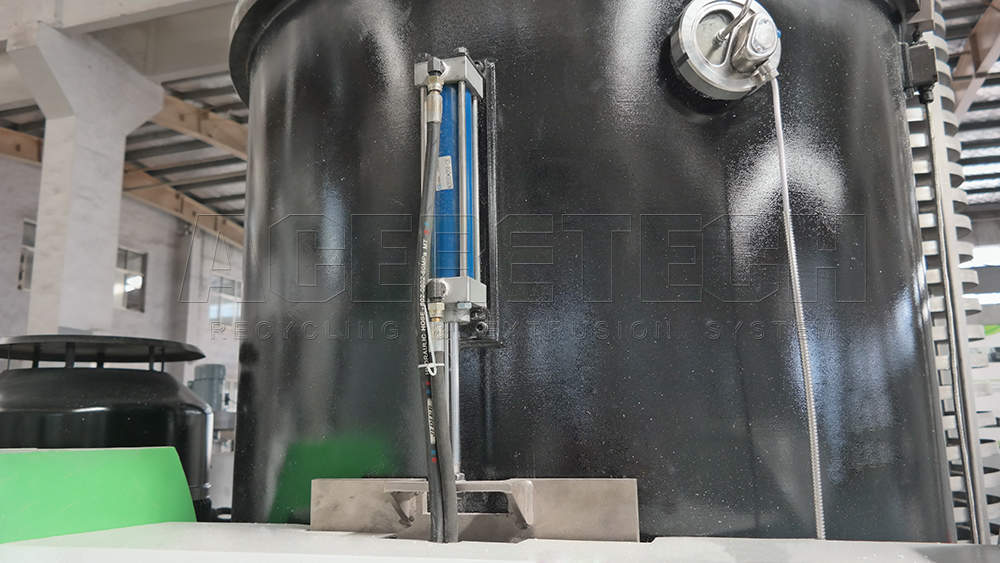
4. Plasticization and degassing: A specialized single screw extruder applied to gently melt the pre-compacted material. The plastic scraps will be well melted, plasticized in a 32 to 34D processing section. With double-zone vacuum degassing system combined with roots pump unit, limit vacuum degassing pressure can be guaranteed reaching -0.1MPa, to remove the volatiles from PET melts maximumly through degassing unit, so as to guarantee tiny IV value reducing.
Â
                                                 Â
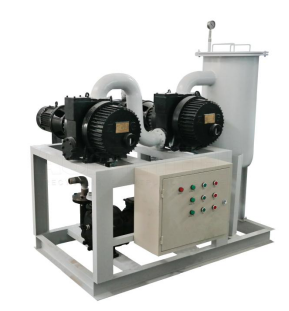
5. Melt filtration: a regular pillar type screen changer is installed on head of extruder to present significant filtration performance. The requirements on the filter technology depend heavily on the quality of the input material as well as the planned use of granules.Â
6. Pelletizing:
Strands pelletizing unit is the typical PET pelletizing method, the strands which come out from extruder's die section, will be manually hauled into the water trough to cool, then, water removed through the air knife device, cut by the rotary blades of pelletizer and form the granules/chips.
Â
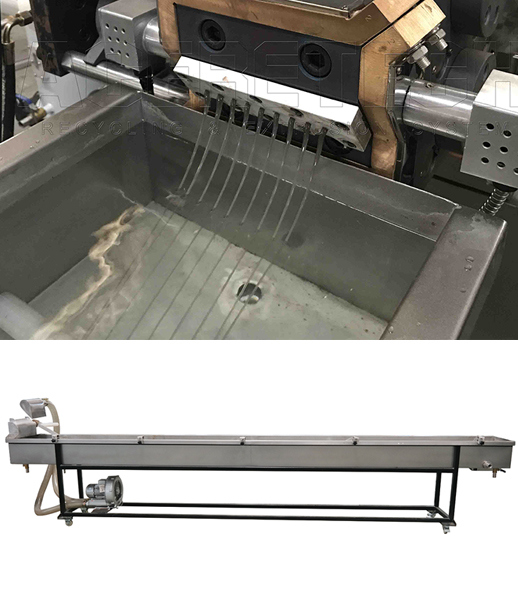
 Main technical parameter:
Machinery size | Data of compactor | Data of single screw extruder |
Throughput   rate(Kg/hr) |
|||
Efficiency volume (Liter) |
Motor power (Kw) |
Diameter of screw(mm) | L/D | Motor power(Kw) | ||
ACS300/80 | 300 | 37 | 80 | 36 | 45/55 | 160-220 |
ACS500/100 | 500 | 55 | 100 | 36 | 90/110 | 300-380 |
ACS800/120 | 800 | 90 | 120 | 36 | 132 | 450-480 |
ACS1000/140 | 1000 | 110 | 140 | 36 | 160/185 | 500-650 |
ACS1200/160 | 1200 | 132 | 160 | 34 | 220/250 | 800-1000 |
ACS1400/180 | 1400 | 315 | 180 | 34 | 315 | 1000-1200 |
ACERETECH: professional equipment manufacture of PET film/flakes/filament re-pelletizing, can provide PET film/flakes/filament re-pelletizing completed solution
Â
Concentration makes profession:Â ACERETECH only focus on studying of waste plastics re-pelletizing technology over the years, has accumulated a wealth of experience on both waste plastics recycling process and related machinery manufacturing ;
Â
Trans-industry coordinating :Â thanks to the coordinate with compounding technology, applying the feature of high volatilization performance from twin screw extruder into PET re-pro process, to assure high efficient degassing performance;
Â
IV value reduced within 0.03 - 0.06 ( test based on clean and dried PET flakes)
Â
Advantages of ACS compacting and pelletizing system
1.Combine crushing, compacting and pelletizing steps in one system, less-labor cost;
2.Higher efficiency feeding, suitable to film, filament, raffia, foaming materials;
3.Higher output and lower energy consumption.
Why choose us
1. Lower investment cost for a high quality and durable machine;
Â
2. Low energy consumption with high production output;
3. Overseas installation and training are available;
4. Machine warranty with spares in stocking and in-time delivery;
Â
5. Fast machine delivery and installation: AceRetech produces on an average of 10 sets of plastic machines per month and can deliver the machine faster than most manufacturers. The regular delivery time of an AceRetech recycling machine is 60 days.
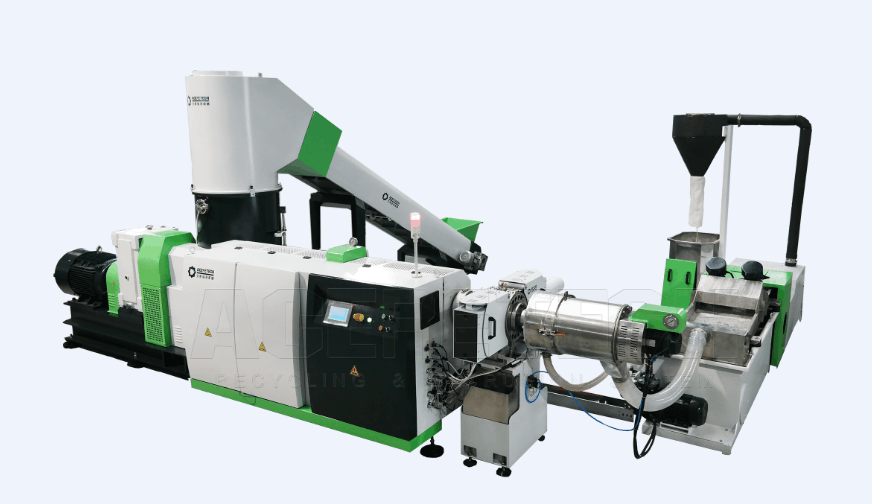
The ACS series compacting and pelletizing system combines function of crushing, compacting, plasticization and pelletizing to one step, applied in the plastics recycling and pelletizing process. ACS system is a reliable and efficiency solution for PP/PE/PET/PVCÂ films, raffias, filaments, PP woven/non woven bags and EPE/EPS/XPS foaming materials re-pelletizing.
Final productions produced by ACS system are in the form of pellets/ granules, can directly put into the production line for film blowing, pipe extrusion and plastics injection, etc.
Specifications:
Model Name | ACS |
Recycling Material | HDPE, LDPE, LLDPE, PP, BOPP, CPP, OPP, PA, PC, PS, PU, EPS, PET |
Final Product Shape | Pellets/ Granules |
System Composition | Belt conveyor, cutting compactor, single screw extruder, pelletizing device, water cooling unit, dewatering section, conveying blower and production silo |
Output Range | 160kg/h-1200kg/h |
Feeding Device | Belt conveyor (standard), Rolls hauling off device (Optional) |
Compactor Volume | 300 Liters-1400 Liters |
Screw Diameter | 80mm-180mm (standard) |
Screw material | 38CrMoAlA nitride steel( SACM-645), bimetallic ( Optional) |
Screw L/D | 34/1, 36/1 (depending on features of recycles) |
Barrel's Heating | Ceramic heater or Casting Aluminum heater |
Barrel's Cooling | Air cooling through fan blowers |
Vacuum Degassing | Double vented degassing with roots pump unit(Standard)Â |
Pelletizing Type | Water cooling strands pelletizing system |
Voltage Standard | Depending on project's location |
Optional Devices | Metal detector, rolls hauling off device, micro feeder for masterbatch, additives, chiller, etc. |
Delivery Time | 60 days after order takes effect. |
Warranty | 13 months since date of bill of lading |
Technical Service | Project design, suggestion on factory construction, installation and commissioning |
Working steps of ACS compacting and pelletizing system
Â
Â
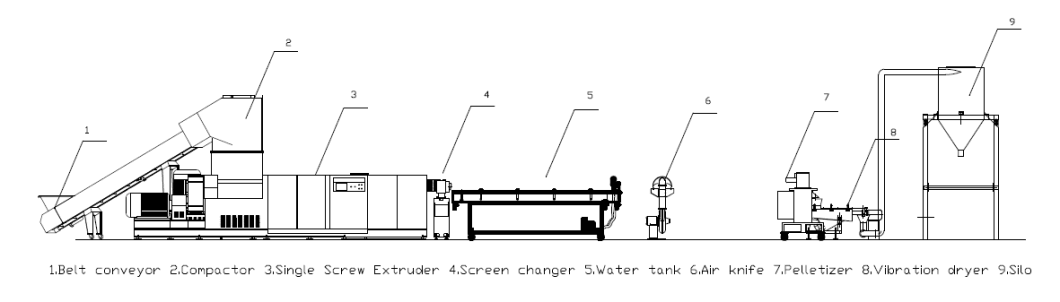
1. Feeding:Â as standard design, plastic scraps such as film, filament, raffias conveyed into the compacting room through belt conveyor; to handle rolls' scraps, roll hauling off device is an optional feeding method. Motor drives of conveyor belt and hauling device cooperate with ABB inverter. Feeding speed of conveyor belt or roll hauling off is fully automatic based on how full the compactor's room is. Metal detector can be combined with belt conveyor, and can interlock with control system, to warn and stop the system, in case that metal is found in feeding section.
2. Crushing and compacting:Â the rotatory blades of compactor will cut up incoming scraps. Frictional heating which caused by high speed rotatory blades will heat and let scraps shrinking just below their agglomerating point. Optimal designed guide structure compacts the material and directs it into extruder screw. Crushes, dries and compacts the material which enables a fast and stable feeding from the compactor directly into the extruder.
Â
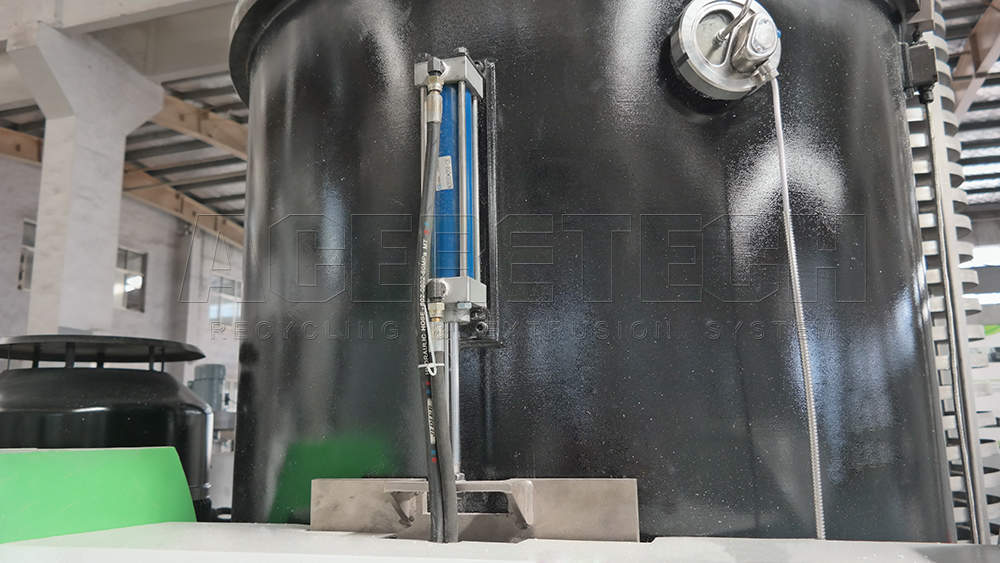
4. Plasticization and degassing: A specialized single screw extruder applied to gently melt the pre-compacted material. The plastic scraps will be well melted, plasticized in a 32 to 34D processing section. With double-zone vacuum degassing system combined with roots pump unit, limit vacuum degassing pressure can be guaranteed reaching -0.1MPa, to remove the volatiles from PET melts maximumly through degassing unit, so as to guarantee tiny IV value reducing.
Â
                                                 Â
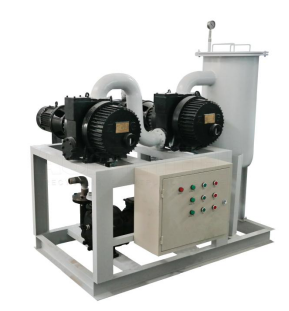
5. Melt filtration: a regular pillar type screen changer is installed on head of extruder to present significant filtration performance. The requirements on the filter technology depend heavily on the quality of the input material as well as the planned use of granules.Â
6. Pelletizing:
Strands pelletizing unit is the typical PET pelletizing method, the strands which come out from extruder's die section, will be manually hauled into the water trough to cool, then, water removed through the air knife device, cut by the rotary blades of pelletizer and form the granules/chips.
Â
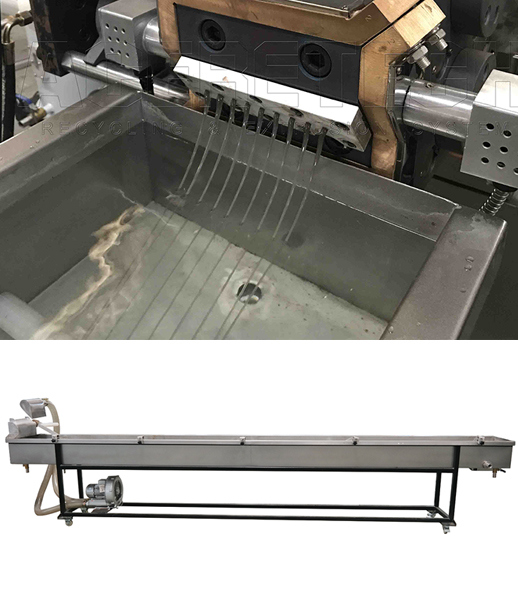
 Main technical parameter:
Machinery size | Data of compactor | Data of single screw extruder |
Throughput   rate(Kg/hr) |
|||
Efficiency volume (Liter) |
Motor power (Kw) |
Diameter of screw(mm) | L/D | Motor power(Kw) | ||
ACS300/80 | 300 | 37 | 80 | 36 | 45/55 | 160-220 |
ACS500/100 | 500 | 55 | 100 | 36 | 90/110 | 300-380 |
ACS800/120 | 800 | 90 | 120 | 36 | 132 | 450-480 |
ACS1000/140 | 1000 | 110 | 140 | 36 | 160/185 | 500-650 |
ACS1200/160 | 1200 | 132 | 160 | 34 | 220/250 | 800-1000 |
ACS1400/180 | 1400 | 315 | 180 | 34 | 315 | 1000-1200 |
ACERETECH: professional equipment manufacture of PET film/flakes/filament re-pelletizing, can provide PET film/flakes/filament re-pelletizing completed solution
Â
Concentration makes profession:Â ACERETECH only focus on studying of waste plastics re-pelletizing technology over the years, has accumulated a wealth of experience on both waste plastics recycling process and related machinery manufacturing ;
Â
Trans-industry coordinating :Â thanks to the coordinate with compounding technology, applying the feature of high volatilization performance from twin screw extruder into PET re-pro process, to assure high efficient degassing performance;
Â
IV value reduced within 0.03 - 0.06 ( test based on clean and dried PET flakes)
Â
Advantages of ACS compacting and pelletizing system
1.Combine crushing, compacting and pelletizing steps in one system, less-labor cost;
2.Higher efficiency feeding, suitable to film, filament, raffia, foaming materials;
3.Higher output and lower energy consumption.
Why choose us
1. Lower investment cost for a high quality and durable machine;
Â
2. Low energy consumption with high production output;
3. Overseas installation and training are available;
4. Machine warranty with spares in stocking and in-time delivery;
Â
5. Fast machine delivery and installation: AceRetech produces on an average of 10 sets of plastic machines per month and can deliver the machine faster than most manufacturers. The regular delivery time of an AceRetech recycling machine is 60 days.
XS wheel spacers and ATV spacer are Made from High-Strength Aluminum Alloy, designed to give your vehicle a wider, more stable stance, quickly and easily. With the right high pe performance Spacers installed, your car takes on a more aggressive look, with the wheels and tires-filling the wheel arches exactly the way they should. XS Spacers are available in a wide range of sizes, from 5mm all the way to 76mm, depending on the application, letting you position your tires exactly where they will look and perform their best. In many cases, installing the right Spacers can improve the look and function of your existing wheels and tires so much, you might not need to buy new custom wheels and tires at all.
Widen Your Stance-For Better Handling
Precision Engineered Hub-Centric and Model Specific for Perfect Fit and Wheel
Balance
Strength-Tested for All Applications
corrosion Protection Through Coating Process-anodizing
Reduced Weight Compared to Steel Wheel Spacers
XS ATV wheel
spacers made by professional manufacturer are designed to give your ATV vehicle
a wider, more stable stance, quickly and easily. Made from High-Strength
Aluminum Alloy, Widen Your Stance-For Better Handling, most popular size: 4-100, 4-110, 4-136, 4-144, 4-156
Hub Centric
Rings, designed to fill in the gap between the hub of the car and the center
bore of the wheel for averting vibration. There are two kinds of material used,
one is PE, another is T6-6061 aluminum.
are
designed to fill in the gap between the hub of the car and the center bore of
the wheel. Most wheel manufacturers design their wheels with a center bore
large enough to fit on most cars. Therefore, since wheel manufactures make
their center bore large enough to fit most cars, most wheel fitments have a gap
between the hub and the center bore.This gap usually doesn't allow for the
wheel to fit hub centric but rather lug centric which causes vibration.
Therefore, to fill the gap and ensure the fitment is hub centric, hub rings are
used.
top quality lug bolts, lug nuts and wheel locks are COLD FORGED and are tempered to strength class 10.9, XS wheel bolts are made from 40Cr or 40CrMo by cold extrusion machine and chrome layer gives the brilliant appearance with grade 10.9 strength, there are conical seat, radius seat, and Allen key style.
Wheel Parts, Wheel Adapter, Atv Wheel Spacers, Wheel Locking Nuts, Wheel Insert
Ningbo Xiangsheng Auto Parts Co., Ltd. , http://www.partsaa.com